3D-MESSTECHNIK
Exakt, zuverlässig & schnell
Gemeinsam mit unserem nach DIN EN ISO/IEC 17025 akkreditierten Kooperationspartner 3DIMETIK können wir Sie bei nahezu jeder messtechnischen Fragestellung unterstützen. Sei es für eine Erstbemusterung, bei Serienmessungen bis hin zum Reverse Engineering.
Wir sind die richtigen Partner für Sie.
Steigern Sie den Nutzen Ihrer Messergebnisse
Mit unseren flankierenden Leistungen finden sie bei uns alles, um den Nutzen aus Ihren Messergebnissen weiter zu steigern.
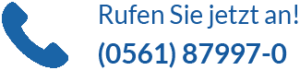
Entlastung Ihrer 3D-Koordinatenmessmaschine
Werkzeugkorrekturen vor Ort ermitteln
Überprüfung v. Betriebsmitteln (Anlagen/Lehren) vor Ort
- B. Braun Melsungen AG
- BorgWarner Turbo Systems GmbH
- Coco Werk GmbH & Co. KG
- u.v.m.
Ihr Ansprechpartner im Bereich 3D-Messtechnik ist
Herr Dipl.-Ing. Mirco Simunovic
UNSER KOOPERATIONSPARTNER IN DER OPTISCHEN 3D-MESSTECHNIK
Das sagen unsere Kunden
„Zusammen mit unserem langjährigen Engineering-Partner casim konnten wir ein innovatives System entwickeln, welches unsere führende Marktposition auch in Zukunft sichert.“
„Wenn es um die volle Wertschöpfungskette geht, bietet unser Engineering-Partner casim alles – von der Idee über die begleitende Berechnung bis hin zur fertigen Konstruktion.“
„Mit der effizienten Unterstützung unseres Engineering-Partners casim ist es gelungen, die Entwicklung unseres neuen Inhalationsgeräts zu beschleunigen, sowie Funktion und Herstellbarkeit weiter zu optimieren.“
Haben Sie noch Fragen oder möchten Sie sich persönlich beraten lassen?
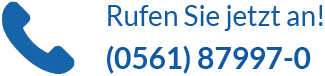
Haben Sie noch Fragen oder möchten Sie sich persönlich beraten lassen?
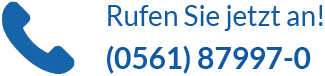
Oder schreiben Sie uns jetzt eine Nachricht:
3D Messtechnik
Zum Thema 3D Messtechnik finden Sie hier unsere Inhalte, nutzen Sie hierfür auch gerne unser Inhaltsverzeichnis mit Schnellinks:
1. Was bedeutet 3D Messtechnik?
2. Messverfahren
2.1 Taktile Messverfahren
2.2 Optische Messverfahren
2.3 Vor- und Nachteile der Messverfahren
3. Reverse Engineering
4. Der Vermessungsingenieur – Bindeglied zwischen Messtechnik und Messergebnis
1. Was bedeutet 3D Messtechnik?
Die Messtechnik im Allgemeinen befasst sich mit Geräten und Methoden zur Messung von physikalischen Größen wie Länge, Gewicht, Druck, elektrischer Widerstand und weiteren mehr. Im Kontext der industriellen Fertigungstechnik und der angegliederten Qualitätssicherung verknüpft man mit der 3D Messtechnik in der Regel die räumliche Vermessung von Werkstücken. Grundsätzlich unterscheidet man zwischen der dimensionellen Messung, der Formmessung sowie der Oberflächenmessung von Werkstücken. Mit der dimensionellen Messung werden Maßabweichungen festgestellt. Formmessungen dienen zur Ermittlung der Gestaltabweichungen von Form- und Lageelementen. Zu den Formelemente gehören z. B. die Geradheit, Ebenheit, Rundheit, Zylindrizität sowie beliebige Linien oder Flächen. Setzt man mindestens zwei von ihnen in Beziehung ergeben sich Lageelemente wie z. B. die Parallelität, Rechtwinkligkeit, Neigungswinkel oder Symmetrie. Um die Abweichungen untereinander abgrenzen zu können, gruppiert man diese in Ordnungsklassen. Diese Ordnungsklassen berücksichtigen die Relation von Periodendauer (Wellenlänge) zum Spitze-Spitze-Wert (Wellentiefe) einer gedachten Welle. So spricht man bei Maß- und Formabweichungen von Grobgestaltabweichungen der ersten Ordnung. Sie stehen für ein Verhältnis von Wellenlänge zur Wellentiefe von über 1000:1. Oberflächenabweichungen, wie Welligkeit und Rauheit gelten als Feingestaltabweichungen. Hierbei wird die Welligkeit als Abweichung zweiter Ordnung (Wellenlänge zu Wellentiefe von 1000:1 bis 100:1) kategorisiert. Rauheiten gelten als Abweichungen dritter bis fünfter Ordnung (100:1 bis 5:1). Nicht jedes System in der Messtechnik ist gleichsam geeignet, Grobgestaltabweichungen und Oberflächenabweichungen zuverlässig zu ermitteln. Man kann sagen, dass mit zunehmender Ordnungszahl der zu ermittelnden Abweichungen die Messtechnik immer spezifischer für den jeweiligen Zweck wird. Grundsätzlich unterscheidet man in der Messtechnik die Systeme dadurch, ob sie den Prüfling mit einem Taster taktil erfassen oder die Abweichungen optisch, und somit berührungslos, ermitteln.
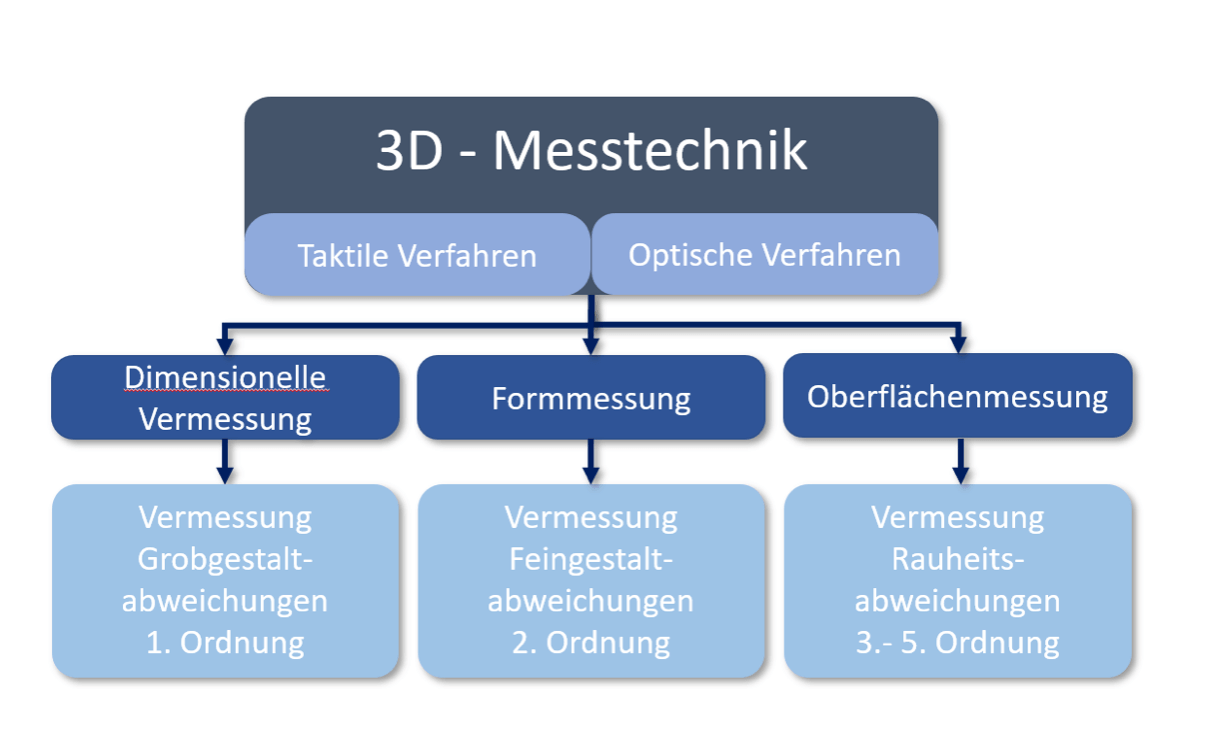
Abbildung: Strukturierung der 3D-Messtechnik
2. Messverfahren
Die Anforderungen an die heutige Messtechnik sind sehr vielfältig. Sie muss zunächst zuverlässig und schnell genaue Messwerte liefern. Verknüpft mit den zunehmenden Genauigkeitsanforderungen an die Bauteile technischer Produkte und den damit einhergehend immer leistungsfähigeren Herstellungsmethoden, nehmen die Forderungen an die Genauigkeiten von Messsystemen stetig zu. Das gleiche gilt auch für die quantitativen Aspekte. Immer mehr Teile sollen umfassender beurteilt werden, idealerweise fertigungsbegleitend – also in einem robusten Umfeld. Anforderungskollektive, die häufig zu einen Zielkonflikt führen. So schließen sich zum Beispiel schnelle Messergebnisse für die fertigungsnahe Bauteilvermessung und höchste Anforderungen an die Messgenauigkeit aus. Es gibt keine Messtechnik, die allen Forderungen voll umfänglich gerecht werden kann. Die Praxis ist dadurch geprägt, dass man unterschiedliche Messsysteme parallel unterhalten muss, um allen Anforderungen gerecht werden zu können.
2.1. Taktile Verfahren
Es existieren sehr unterschiedliche Ausführungen von taktilen Messsystemen. Es gibt hoch spezialisierte Messtechnik zum Beispiel in Form von Formmessgeräten oder Oberflächenmessgeräten (sog. Tastschnittgeräte). Sie zeichnen sich dadurch aus, dass sie für die jeweilige Aufgabe optimal ausgelegt sind und Messungen mit ausordentlich hohen Genauigkeiten ermöglichen. Koordinatenmessgeräte sind universeller einsetzbar. Sie beruhen auf dem Prinzip der Koordinatenmesstechnik, welche die Raumkoordinaten in X-, Y- und Z-Richtung von Messpunkten zur Ermittlung von Bauteilabweichungen auswertet. Über ein Verfahr- bzw. Positioniersystem wird der Messtaster durch den Messraum des Messsystems bewegt. Kommt ein schaltender Messtaster zum Einsatz, wird dieser gegen die Oberfläche des Prüflings gedrückt, so dass ein Schaltimpuls auslöst. Mit Hilfe geeigneter Hard- und Softwarekomponenten werden die Raumkoordinaten des Tasters im Schaltzustand ermittelt und ausgewertet. Messende Messtaster hingegen haben einen Taststift, der federnd beweglich gelagert ist. Dieser wird während des Messvorgangs kontinuierlich gegen die Oberfläche des Prüflings gedrückt und somit die zu messende Oberfläche „gescannt“. Die Bauteilabweichung wird über den Relativabstand zwischen Schaltpunkt und Nullpunkt des Tasters sowie über die absolut gemessene Position des Handhabungssystems ermittelt.
2.2. Optische Messverfahren
In den vergangenen Jahren haben die optischen Messverfahren in der 3D Messtechnik zunehmend an Bedeutung gewonnen. Der häufigste Anwendungsfall ist im Zusammenhang mit den optischen Messverfahren die Vermessung von sichtbaren Oberflächen. Das Grundprinzip der optischen 3D Messtechnik ist die digitale Bildverarbeitung. Mit Hilfe von leistungsfähigen Kamerasystemen und Objektiven werden beleuchtete Prüflinge (Stichwort: Streifenlicht) fotografisch erfasst. Über zugehörige Software-Tools werden aus den zweidimensionalen, digitalen Bildern 3D-Geometrien errechnet, welche dann mit den Nominalgeometrien aus dem CAD Programm verglichen werden können. Die Abweichungen der gemessenen IST-Geometrien in Relation zu den Daten der CAD Programme (entspricht der SOLL-Geometrie) wird farblich kodiert dargestellt, ähnlich der Ergebnisdarstellung bei der Finite Element Methode (FEM). Um bekannten Störgrößen bei der Messung entgegenzuwirken, kann dieses Prinzip variiert werden. So können zum Beispiel spezielle Lichtquellen eingesetzt werden, um dem negativen Einfluss von Streulicht entgegen zu wirken.
Der neueste Trend in der optischen 3D Messtechnik ist die Computer Tomographie (kurz: CT). Die aus der Medizintechnik bekannte Technologie zur bildgebenden Diagnose wurde in den vergangenen Jahren so weiterentwickelt, dass sie auch in der industriellen 3D Messtechnik hinsichtlich Handhabung und Kosten einsetzbar ist. Mit dem CT wird der Prüfling inkrementell mit Röntgenstrahlen durchleuchtet. Die so entstehenden Schnittbilder können nun wieder mittels Software zu einem dreidimensionalen (Volumen-)Datensatz zusammengesetzt werden. Auf diese Weise können neben den Oberflächen auch die inneren Strukturen des Prüflings digital in 3D abgebildet werden.
2.1 Taktile Messtechnik
Der wesentliche Vorteil der taktilen Messtechnik ist die sehr hohe Genauigkeit, mit denen sie Abweichungen erfassen kann. So sind mit 3D Koordinatenmessgeräten Genauigkeiten im Bereich von Mikrometer erreichbar. Voraussetzung ist natürlich, dass die technische Ausführung der Messtechnik (Messtisch, Verfahreinheiten, Messköpfe) von hoher Güte sind. Zudem muss auch die Infrastruktur, also die Lage des Messraums, wie auch dessen Klimatisierung den Forderungen entsprechend ausgelegt sein. Formmessgeräte, die auf die Vermessung rotationssymmetrischer Geometrien (Ebenen, Zylinder, Kegel) spezialisiert sind, erreichen Genauigkeiten im Sub- Mikrometerbereich. Noch höhere Genauigkeiten in der Ermittlung von Abweichungen (im Nanometer-Bereich) sind mit sogenannten Tastschnittgeräten möglich, mit denen Rauheits- und Konturmessungen durchgeführt werden. Wenn die Genauigkeitsanforderungen nicht zu hoch sind, können taktile Messsysteme, zum Beispiel eine Portalmessmaschine, auch fertigungsnah zur produktionsbegleitenden Werkstückvermessung eingesetzt werden. Immer wiederkehrende Vermessungen gleicher Werkstücke kann mit entsprechenden Messhilfsmitteln und Aufnahmevorrichtung im hohen Maße standardisiert und so vereinfacht werden, so dass zur Durchführung nicht zwangsläufig ein Vermessungsingenieur erforderlich ist. Die größten Nachteile der taktilen Messtechnik sind die zum Teil enormen Investitionskosten bei der Anschaffung der Messtechnik sowie der Infrastruktur. Diese Kosten steigen überproportional mit den Genauigkeitsanforderungen. Auch aus technischer Sicht gibt es Beschränkungen. Die Vermessung komplexer Werkstücke bedingt häufig eine zeitaufwendige Aufnahme und Ausrichtung des Werkstückes im Messsystem sowie die Generierung geeigneter Messprogramme. Aufwendungen, die einer schnellen Bauteilvermessung im Wege stehen. Verschärft wird die Situation um die Messdauer, wenn das Messsystem lange Verfahrwege zurückzulegen hat und Punkte aufwendig angetastet werden müssen. Ferner ist die Vermessung nicht ausreichend steifer Werkstücke (zum Beispiel Dichtlippen) mittels taktiler Messtechnik kaum möglich. Auch die Beschädigung höchst Empfindlicher Oberflächen (zum Beispiel Beschichtungen) durch die Taster könnte ein Problem in der Praxis darstellen.
2.2 Optische Messtechnik
Die optischen Messverfahren verbuchen einige wichtige Vorteile für sich. Zunächst sind die Geräte für die optischen Messverfahren in Relation zu den taktilen Geräten relativ preisgünstig in der Anschaffung. Allerdings müssen die CT-Geräte von dieser Aussage ausgenommen werden. Ein weiterer Vorteil, der die Entscheidung für diese Art Messverfahren entscheidend mit prägt ist, dass die Beurteilung von flächigen Abweichungen ohne größeren messtechnischen Mehraufwand sehr gut möglich ist. Der Vergleich geschieht durch die Überlagerung der aus den Messungen entstandenen 3D-Daten mit denen des idealen CAD-Konstruktionsdatensatzes. Die Referenzierung (der Nullabgleich) der Datensätze erfolgt über gemeinsame Bezugssysteme. So werden alle Abweichungen in Relation zu den festgelegten (Mess-)Bezugssystemen ausgewiesen. Diese Informationen stehen somit in Analogie zu den zonenbasierenden Tolerierungen der geometrischen Produktspezifikation (GPS). Durch relativ einfach umsetzbare Modifikationen an den Bezugssystemen lassen sich schnell die Auswirkungen veränderter Montage- und Prüfkonzepte beurteilen. Diese Flexibilität in der Datenauswertung ist ein weiterer wesentlicher Vorteil der optischen Messverfahren. Größere Strukturen, wie zum Beispiel eine Fahrzeugkarosserie, lassen mit mobilen Geräten direkt in der Fertigung vermessen, ohne dass besondere Anforderungen an die Umgebung bestehen. Kleine und kleinste Werkstücke hingegen müssen, ähnlich wie bei den taktilen Messverfahren, mit geeigneten Messhilfsmitteln bzw. Vorrichtungen aufgenommen werden, um so zu nutzbaren Messbezügen kommen zu können. Berührungslose Messung bedeutet auch, dass selbst Werkstücke mit geringer Steifigkeit, wie zum Beispiel Dichtlippen, im Grunde problemlos mit der optischen Messtechnik beurteilt werden können. Die Dauer eines Messprozesses bei der Vermessung von Oberflächengeometrien mit den optischen Messverfahren ist im Vergleich zu den taktilen Messverfahren sehr kurz. Dies ist ein wichtiger Aspekt, wenn es darum geht, dass in kurzer Zeit viele Bauteile vermessen werden sollen. Dieser Zeitvorteil nimmt jedoch ab, wenn der Prüfling aufwendig in eine Messvorrichtung aufgenommen werden muss oder ein CT zum Einsatz kommt.
Neben den vielen und für die fertigungsnahe Qualitätssicherung so wichtigen Vorteilen hat die optische Messtechnik auch handfeste Nachteile. Zunächst einmal stellen stark reflektierende Oberflächen ein Problem dar, weil die entstehenden Lichtreflexe zu Fehlinterpretationen führen. Ein ähnliches Problem besteht, wenn Kunststoffwerkstücke nur geringe Wandstärken haben, so dass sie von der beleuchtenden Lichtquelle durchleuchtet und die Messergebnisse dadurch verfälscht werden. Gilt es abgeschattete Geometrien, wie zum Beispiel tiefe Sacklöcher oder Kühlrippen zu messen, ist dies nur über Umwege oder dem Einsatz von Hilfsmitteln (zum Beispiel einen Kerndorn) möglich. Je kleiner die zu vermessenden Strukturen werden, desto wichtiger wird das Auflösungsvermögen des optischen Messsystems. Kleinste Strukturen werden womöglich so schlecht aufgelöst, dass zum Beispiel Kreisgeometrien (Bohrungen) als Vielecke dargestellt werden. Die fehlende Möglichkeit, aus solch einem Vieleck einen – und zwar den richtigen – Mittelpunkt zu ermitteln, führt im Vergleich zu den taktilen Messverfahren zu relativ großen Ungenauigkeiten in den Messergebnissen.
2.3. Vor- und Nachteile der Messverfahren
Die Frage nach dem richtigen oder besseren Messverfahren, lässt sich nicht allgemeingültig mit taktil oder optisch beantworten. Beide Verfahren haben ausgeprägte Stärken und unvermeidbare Schwächen.
3. Reverse Engineering
In der Konstruktion gewinnt zunehmend das Reverse Engineering an Bedeutung. Im Kontext zur 3D Messtechnik steht Reverse Engineering dafür, dass die digitalen Oberflächendaten der optischen Bauteilvermessungen in das CAD Programm zurückgeführt werden. Basierend auf den so vorliegenden CAD Daten kann der Konstrukteur nun Details des Werkstückes den veränderten Anforderungen anpassen. Reverse Engineering ist insbesondere dort attraktiv, wo von real vorliegenden Werkstücken/Bauteilen keine Konstruktionsdaten für das CAD Programm vorliegen. Hier kann der Prozess des „Nachkonstruieren“ erheblich beschleunigt werden, so dass mit Abschluss der Konstruktion alle notwendigen Konstruktionszeichnungen vorliegen, was die Vorbedingung für die Nachfertigung von zum Beispiel Bauteilen oder Vorrichtungen ist.
4. Der Vermessungsingenieur – Bindeglied zwischen Messtechnik und Messergebnis
Jede Messung unterliegt Störgrößen, welche sich als Messfehler niederschlagen. Die Ursachen dieser Störgrößen lassen sich zum einen der Messtechnik zuordnen, zum anderen begründen sie sich aus dem Messprozess. Somit beeinflusst also die Person, die die Messtechnik bedient, die Qualität der Messungen. Ein ausgebildeter Messtechniker – denkbar wäre auch ein Vermessungsingenieur – wäre somit, genauso wie eine technisch leistungsfähige 3D Messtechnik, eine wichtige Voraussetzung für eine qualitativ hochwertige Bauteilvermessung. In Deutschland gibt es zurzeit keinen anerkannten Ausbildungsberuf zum Messtechniker. Auch an den Hochschulen gibt es keinen Studiengang, der explizit zum Vermessungsingenieur in 3D Messtechnik führt. Sicherlich werden in dem ein oder anderen Institut Themen wie 3D Messtechnik, Bauteilvermessungen und Artverwandtes mehr oder weniger intensiv aufgegriffen. Aber einen qualifizierten Abschluss gibt es in diesem Bereich der Qualitätssicherung nicht. In aller Regel findet die Ausbildung zum Messtechniker, zum Vermessungsingenieur auf betrieblicher Ebene statt. So verfügt jeder Hersteller von Messgeräten und Messtechnik auch über ein umfangreiches Angebot an Aus- und Fortbildung. Der Fokus dieser produktnahen Schulungen liegt zunächst in der fachgerechten Bedienung der (erworbenen) Messtechnik – was sicherlich nicht falsch ist. Zur weiteren Ausbildung sollte jedoch auch gehören, dass intensiv geschult wird, wie die aufwendig generierten Messdaten zu filtern und auszuwerten sind. Denn nur so erlangt man die richtigen Erkenntnisse hinsichtlich der Einhaltung der geforderten Spezifikationen. Grundvoraussetzung für diesen Schritt jedoch ist, dass der Messtechniker/ der Vermessungsingenieur auch die zu Grunde liegenden Zeichnungen lesen kann, also die Symbolsprache der geometrischen Produktspezifikation (GPS) kennt und versteht. In der industriellen Messtechnik werden häufig nicht nur einzelne Werkstücke vermessen und geschaut, ob die Messwerte innerhalb der Spezifikationen liegen. Viel häufiger werden Messreihen gefahren, um Fertigungsprozesse zu steuern, oder deren Leistungsfähigkeit zu beurteilen. Damit dies gelingen kann, müssen die Messdaten in aller Regel noch statistisch aufbereitet und zum Beispiel in Form von Maschinenfähigkeit Cm bzw. Maschinenfähigkeitskennwert Cmk oder Prozessfähigkeitsindex Cp bzw. kleinsten Prozessfähigkeitsindex Cpk ausgewertet werden. Auch wenn es sehr gute Software Tools gibt, die diese Aufgabe erledigen, braucht es auch Kenntnisse aus dem Themenfeld Statistik. Erst damit können die Parameter zur statistischen Auswertung richtig gewählt und die Ergebnisse interpretiert werden.
Zusammenfassend muss der Messtechniker, der Vermessungsingenieur folgende Qualifikationen haben:
Bedienung der 3D Messtechnik
Filterung und Auswertung von Messdaten
Kenntnisse in geometrischer Produktspezifikation (GPS)
Kenntnisse in Statistik (Prozessfähigkeitsindizes)
Somit wird deutlich, dass die Anforderungen an den Messtechniker, dem Vermessungsingenieur weit über die Bedienung der 3D Messtechnik hinausgeht.
Quellen: